
A hexagonal pattern was used to layer Kevlar sheets to later be formed in to the appropriate shape to get the desired curvature of the helmet

The group utilized the School of Engineering's Paint booth to apply a vinyl coating to the helmet shell used to provide a prototype

The image below is of molds currently being used to fabricate sample in impact and tensile testing

Depicted below are sample used to help the group troubleshoot heat source, temperatures and time exposed to heat

Samples below are of varying UHMWPE/Kevlar composition and formed at set temperatures and times as determined by troubleshooting process

Vacuum sealing samples has been utilized as shown below to minimize the risk of impurities caused by air pockets withing the samples

The current design for the prototype is not unique to helmets. The process by which the helmet is made is dependent upon testing results and to be determined. Currently the group is exploring parallel options for both molding and 3D printing using kevlar and UHMWPE composites. Samples will be tested and fabricated using the above mentioned processes.
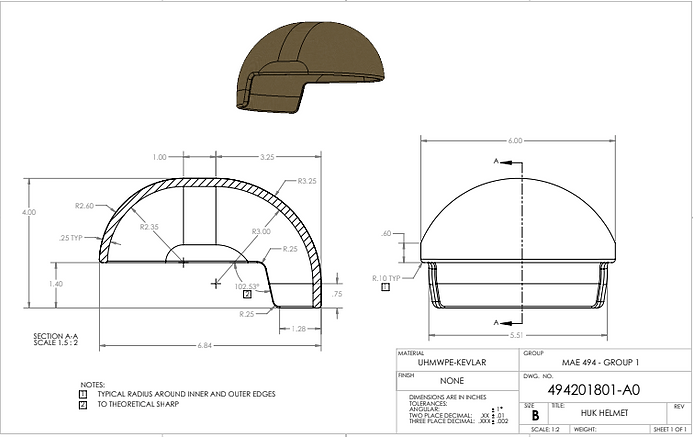